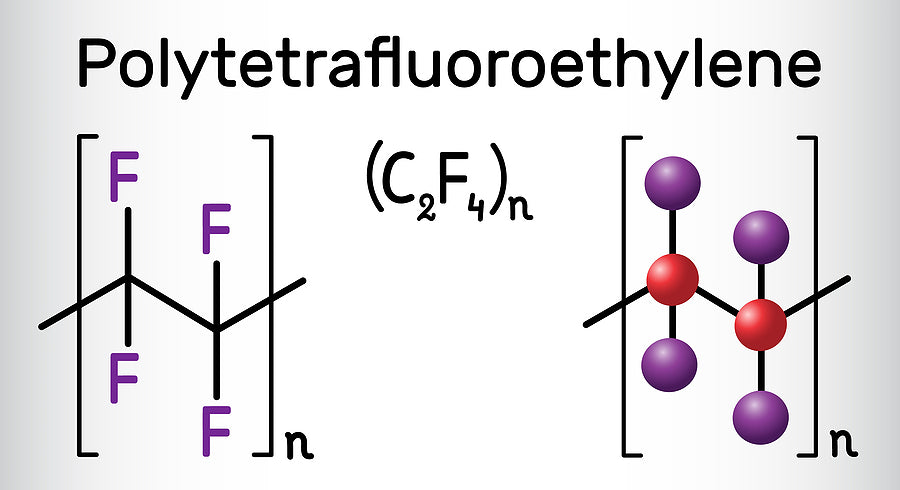
How is a vent manufactured?
Here we look at a very rough outline of how a vent is created, it is not a precise list as some of the manufacturing processes are specific to each manufacturer and as is always the case, "all manufacturers are equal - but some are more equal than others....!"
Nitto Denko is a renowned manufacturer known for its range of products, including PTFE (Polytetrafluoroethylene) membrane vents, commonly referred to as "Temish" vents. Below, we provide an overview of the production methods for PTFE membrane vents and the factors that influence their airflow characteristics.
-
1. Material Selection: The production of PTFE vents begins with the selection of high-quality PTFE material, known for its exceptional resistance to harsh environmental conditions, making it suitable for venting applications.
2. Membrane Formation and Microstructure Control:
a. Paste Extrusion or Compression Molding: The process starts with PTFE resin in the form of a fine powder or paste. Manufacturers can use methods such as paste extrusion or compression molding to form a solid sheet of PTFE.
b. Porosity Creation: The next step involves creating the desired porosity or porous structure within the PTFE through a process known as "expansion" or "stretching."
c. Stretching Process: The heated PTFE sheet is mechanically stretched, elongating the PTFE molecules and creating microscopic voids within the material, resulting in a porous structure. Stretching can be controlled to achieve specific pore sizes, and direction and degree of stretching can impact the membrane's properties.
d. Microstructure Control: Several factors influence the microstructure of the PTFE membrane, including temperature, stretching ratio, orientation, and cooling or quenching. These factors are carefully controlled to achieve the desired pore size, distribution, and overall microstructure.
e. Calibration and Testing: Quality control measures, including microscopy and pore size measurement, are used to calibrate and verify that the resulting membrane meets the desired specifications for airflow, porosity, and filtration performance.
3. Hydrophobic and Oleophobic Treatment: Additional hydrophobic and oleophobic treatments may be applied to enhance the inherent properties of PTFE, ensuring that the vent repels water and oils effectively.
4. Adhesive and Assembly: PTFE membranes are often attached to a substrate or housing using adhesive bonding techniques. The design of the housing can also influence the airflow characteristics of the vent, including factors like the number and size of vent openings.
5. Quality Control: Rigorous quality control measures are employed throughout the manufacturing process to ensure the vents meet specific airflow and performance requirements. This includes testing the vents for their ability to block liquids, filter particles, and allow airflow at the desired rates.
6. Customization for Airflow: The specific airflow characteristics of a PTFE membrane vent can be customized based on the application's needs. Adjustments to factors like pore size, membrane thickness, and overall vent design can achieve the desired airflow rate. Vents with greater airflow typically have larger pores or a larger membrane surface area.
7. Custom shapes: The default standard shape for most vents is round, an outer ring is where the adhesive substrate sits, leaving the inner section free to perform its purpose. Custom shape can be created so the vent fits into specific sizes of the device, such as a long thin oval shape for a mobile phone speaker.
It's important to note that the precise production methods and proprietary techniques used by Nitto Denko for their Temish vents may vary and are not publicly disclosed. However, they likely employ advanced manufacturing processes and quality control procedures to meet the diverse needs of their customers for various venting applications.
Selectronix Onboard Ltd
0118 9817387
copyright 10/10/23